
ПУБЛИКАЦИИ
АВТОМАТИЗИРОВАННАЯ ВИХРЕТОКОВАЯ СИСТЕМА ELO 3T ДЛЯ КОНТРОЛЯ ОБОЛОЧЕК ТВЭЛОВ
МАРЧЕНКО Виктор Григорьевич, Руководитель группы технологического контроля АО «НЗХК-Инжиниринг», Новосибирск,
НОРЧЕНКО Юрий Григорьевич, Ведущий инженер группы технологического контроля АО «НЗХК-Инжиниринг», Новосибирск,
СЕМЕРЕНКО Алексей Владимирович, Руководитель отдела средств НК и ТД, ООО «Панатест», Москва,
ЧАЩИН Сергей Борисович, Начальник конструкторского бюро неразрушающих средств контроля АО «НЗХК-Инжиниринг», Новосибирск.
Главным конструктивным элементом активной зоны гетерогенного ядерного реактора является тепловыделяющий элемент (твэл). В твэлах происходит деление тяжелых ядер 235U, 239Pu или 233U, сопровождающееся выделением тепловой энергии, которая затем передается теплоносителю. Твэлы состоят из топливного сердечника, оболочки и концевых деталей.
К качеству твэлов, используемых в реакторе, предъявляются очень жесткие требования. Твэлы энергетических реакторов должны быть тщательно обследованы и испытаны до установки в тепловыделяющую сборку, чтобы обеспечить правильную работу реактора, его безопасность.
Один из основных параметров, определяющих технические характеристики твэлов, – целостность оболочки, так как именно она является главной частью защиты теплоносителя и окружающей среды от попадания продуктов деления. Наибольшее распространение в энергетических реакторах получили оболочки трубчатого типа, изготавливаемые из сплавов циркония или нержавеющей стали.
Оболочки твэлов находятся в сложных условиях эксплуатации. Они подвергаются тепловому, химическому и механическому воздействию. В современных методах дефектоскопии твэлов и тепловыделяющих сборок широко используется вихретоковый метод.
Дефекты, обнаружение которых является целью испытаний, можно разделить на три группы:
1) первичные дефекты, возникшие в процессе производства материала. К ним относятся изменения химического состава, поверхностные и внутренние трещины;
2) дефекты, обусловленные технологическим процессом изготовления реакторных деталей (получение заготовки, механическая обработка и термообработка). К этим дефектам относятся пористость, разрывы, трещины;
3) дефекты, возникшие при сборочных операциях. По заказу одного из отраслевых предприятий компанией АО «НЗХК-Инжиниринг» была разработана автоматизированная вихретоковая установка для контроля трубчатых оболочек твэлов.
ТЗ заказчика содержало следующие требования:
- длина контролируемых труб 4000 ± 2 мм;
- диаметр 9,10 ± 0,04 мм;
- скорость перемещения труб через позицию контроля 180 ± 10 мм/с.
Вероятность выявления искусственных дефектов глубиной 0,05 мм должна составлять:
- продольной риски протяженностью 3 мм с углом раскрытия 90° – не менее 0,95;
- поперечной риски протяженностью 3 мм с углом раскрытия 90° – не менее 0,95;
- сферической вмятины радиусом 10 мм – не менее 0,95.
В качестве электронного блока установки был выбран высокоскоростной вихретоковый дефектоскоп модульного типа ELOTEST PL500 производства фирмы Rohmann, Германия (рис. 1).
Технические характеристики вихретокового дефектоскопа модульного типа ELOTEST PL500 (Rohmann, Германия):
- 16 слотов для функциональных модулей различного назначения – измерения, компенсации изменения зазора, мультиплексирования датчиков, ввода-вывода;
- до 256 каналов для работы с вихретоковыми матрицами;
- одновременное отображение до 8 сигналов на цветном ЖК-дисплее с диагональю 229 мм и разрешением 800×480 пикселей;
- частотный диапазон 10 Гц–12,5 МГц;
- полностью цифровая обработка сигналов с дискретизацией 250 кГц с предельно низким уровнем шума и стабильностью результатов;
- усиление 16–80 дБ с регулируемым шагом 0,5 дБ;
- предусиление 16,5–80 дБ.
В состав механической части установки (рис. 2) вошли: стол 1; протяжка 2 (2 шт.); центратор 3 (4 шт.); укрытие 4 (2 шт.); двухканальный вращающийся вихретоковый датчик EC производства Rohmann (далее датчик EC) 5; блок вихретокового преобразователя производства Rohmann (далее блок ВТП) 6; блок подготовки воздуха 7; пневмораспределитель 8 (2 шт.); глушитель 9 (4 шт.); фундаментный угловой соединитель 10 (4 шт.); система обработки информации и управления установки контроля внешнего вида твэлов (далее – СОИУ).
В состав СОИУ вошли: шкаф компьютерный; монтажная панель 21; частотный преобразователь 22 (2 шт.); частотный преобразователь 23. В установке применяются два типа вихретоковых преобразователей (ВТП): проходной Rohmann (смонтирован в блоке ВТП); накладной Rohmann (два ВТП в датчике ЕС).
Вся поверхность оболочки контролируется при протягивании твэла сквозь ВТП. Проходной ВТП служит для выявления крупных дефектов (вмятин) и поперечных рисок, а также для задания начальной точки отсчета расстояния при определении положения дефекта на оболочке твэла.
Зона контроля накладными ВТП, вмонтированными в ЕС, представляет собой участок по верхности размером приблизительно 2×2 мм. Накладные ВТП, вращающиеся вокруг твэла при его движении вдоль оси, сканируют поверхность по двум спиралям. Накладные ВТП, имеющие меньшую зону контроля, чем проходной ВТП, служат для выявления более мелких дефектов (наколов, забоин) и продольных рисок.
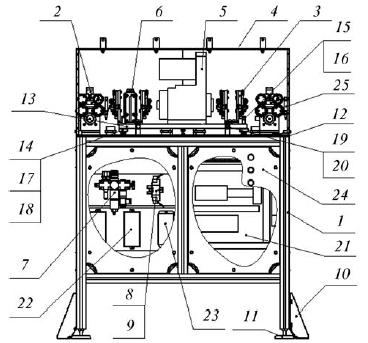

Рис. 2. Механическая часть вихретоковой системы ELO 3T: 1 – стол; 2 – протяжка; 3 – центратор; 4 – укрытие; 5 – датчик ЕС; 6 – блок ВТП; 7 – блок подготовки воздуха; 8 – пневмораспределитель; 9 – глушитель; 10 – фундаментный угловой соединитель; 11 – регулируемая опора; 12 – плита; 13 – плита (регулируемая); 14 – шпилька; 15 – гайка (фиксирующая); 16 – шайба; 17 – гайка (регулировочная); 18 – шайба; 19 – винт (регулировочный); 20 – гайка (контргайка); 21 – монтажная панель; 22 – частотный преобразователь двигателя протяжки; 23 – частотный преобразователь двигателя датчика ЕС; 24 – панель стола; 25 – датчик наличия изделия.
Блок ВТП 6 (см. рис. 2) и датчик ЕС 5 смонтированы на регулируемой плите 13 стола 1. На этой же плите смонтированы четыре центратора 3, служащие для ориентации твэла по оси датчика ЕС и блока ВТП. Две протяжки 2, расположенные на противоположных краях неподвижной плиты 12 стола, обеспечивают прием твэла с рольганга и перемещение через установку.
Нижние ролики протяжки соединены с двигателем зубчатой передачей. Верхние ролики протяжки с помощью пневмопривода прижимают твэл к нижним (тянущим) роликам для обеспечения равномерного движения (без проскальзывания). На каждой протяжке установлены датчики угловых перемещений для определения расстояния от начала твэла до выявленного дефекта. Для этого ось датчика угловых перемещений стыкована с осью прижимного ролика. На выходе протяжек установлены датчики наличия изделия 25 (см. рис. 1).
В исходном состоянии твэл в установке отсутствует, что определяется по датчикам наличия изделия на входной протяжке (протяжка 1) и на выходной протяжке (протяжка 2). Прижимные ролики протяжек находятся в верхнем положении. Два датчика, расположенные на транспортном столе, подающем изделия на установку, подтверждают отсутствие твэла перед установкой.
Дефектоскоп с подключенным к нему проходным ВТП и датчиком ЕС включен и настроен, двигатель датчика ЕС работает.
СОИУ выдает сигнал «Готовность прибора» на систему управления (СУ) загрузки. СУ загрузки при отсутствии твэла на входе установки транспортной, расположенной за установкой контроля, подает на СОИУ сигнал «Изделие принять». СОИУ запускает двигатели протяжек установки. Транспортный стол, расположенный перед установкой, подает твэл по рольгангу на протяжку 1 установки. При входе твэла в зону действия датчика наличия изделия протяжки 1 СОИУ запускает пневмопривод прижимных роликов протяжки 1, при этом подача твэла транспортным столом прекращается. Твэл, прижатый к тянущим роликам протяжки, движется через блок ВТП и датчик ЕС. При входе твэла в проходной ВТП начинается опрос датчика угловых перемещений, смонтированного на протяжке 1. При этом СОИУ начинает прием данных дефектоскопа и их сохранение.
Когда твэл достигает датчика наличия изделия протяжки 2, пневмопривод протяжки 2 опускает прижимные ролики, пневмопривод протяжки 1 поднимает прижимные ролики, начинается опрос датчика угловых перемещений протяжки 2. Одновременно включается транспортная установка линии для приема выходящего из установки твэла. Дальнейшее перемещение твэла происходит с помощью протяжки 2. При выходе твэла за пределы датчика наличия изделия протяжки 2 пневмопривод поднимает прижимные ролики, запись данных прекращается, твэл продолжает двигаться посредством транспортной установки линии.
По окончании контроля проводится обработка сохраненных данных. На время обработки данных СОИУ выдает сигнал «Обработка результата» на СУ загрузки.
Значение сигнала от дефекта, превышающее заданный порог, сохраняется с соответствующим ему расстоянием от начала твэла. Результат обработки данных передается на верхний уровень АСУТП.
Установка имеет пять режимов работы:
- «Комплексный»;
- «Опробование»;
- «Калибровка»;
- «Настройка»;
- «Транспортный».
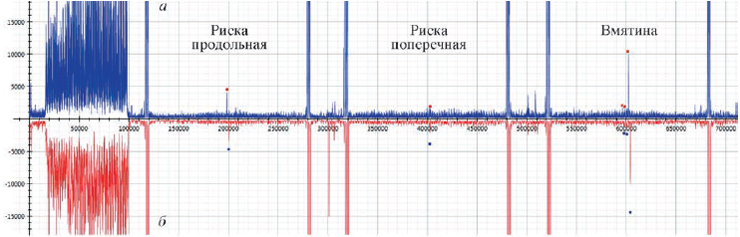

Рис. 3. Дефектограмма СОП, построенная по данным двухканального вращающегося датчика: а – канал 1; б – канал 2.
Режим «Комплексный» предназначен для контроля труб в автоматическом режиме и обмена информацией с АСУТП. Возможна работа (контроль твэлов) без взаимодействия с АСУТП с сохранением результатов контроля в локальной базе данных.
Режимы «Опробование», «Калибровка» и «Настройка» являются режимами автономной работы установки (без взаимодействия с АСУТП).
Режим «Опробование» предназначен для проверки работоспособности установки и ее метрологической исправности.
Режим «Калибровка» служит для определения метрологических характеристик при проведении аттестации и калибровки установки в соответствии с методикой калибровки.
Режим «Настройка» предназначен для настройки и тестирования аппаратной части установки.
Режим «Транспортный» служит для перемещения изделий через установку без проведения контроля.
В процессе приемо-сдаточных испытаний вероятность обнаружения искусственных дефектов, выполненных в виде стандартного образца предприятия (СОП) с размерами дефектов, соответствующими техническому заданию, составила Р=1,0.
На рис. 3, 4 представлены дефектограммы одного из результатов контроля СОП накладными и проходными датчиками.
Так же в процессе приемо-сдаточных испытаний проводили контроль твэлов, прошедших контроль внешнего вида службой ОТК предприятия:
- твэл № 1 – точечный дефект в виде накола глубиной ~0,070 мм (брак);
- твэл № 2 – точечный дефект в виде накола глубиной ~0,090 мм (брак);
- твэл № 3 – потертость размером 18×5 мм глубиной ~0,010 мм (годный).
Каждый твэл был проконтролирован по пять раз. Точечные дефекты были обнаружены при каждом проходе твэлов. Потертость на трубе № 3 не вызывала заметного повышения сигнала. На рис. 5 представлены дефектограммы изделий.
После проведения приемо-сдаточных испытаний установка ELO 3T была принята в эксплуатацию.
Статья опубликована в журнале "Территория NDT", июль-сентябрь 2016.
Загрузить статью в формате PDF...