
ПУБЛИКАЦИИ
КОНТРОЛЬ СВАРНЫХ СОЕДИНЕНИЙ ВИХРЕТОКОВЫМ ДЕФЕКТОСКОПОМ ELOTEST M3/WELD
СЕМЕРЕНКО Алексей Владимирович, Руководитель отдела средств НК и ТД, ООО «Панатест», Москва.
БОГОМОЛОВ Иван Александрович, Инженер, ООО «Панатест», Москва.
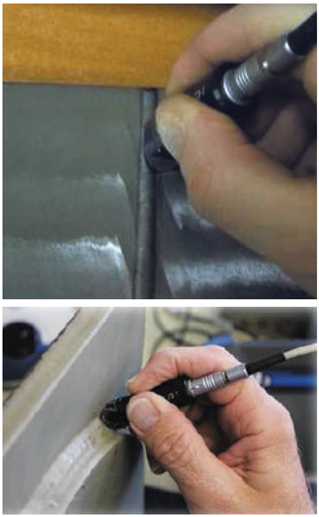

Рис. 1. Вихретоковый контроль сварных соединений.
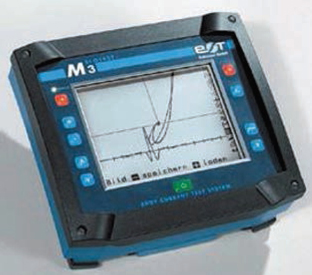

Рис. 2. Внешний вид вихретоковогодефектоскопа Elotest M3.
В настоящее время вихретоковые приборы и установки широко используются для обнаружения и определения параметров несплошностей материалов, контроля размеров напряженно-деформированного состояния объ екта контроля (ОК), физико-механических характеристик структурного состояния материалов и др. Объектами вихретокового контроля (ВТК) могут быть электропроводящие материалы – прутки, проволока, трубы, листы, железнодорожные рельсы, корпуса атомных реакторов, подшипники, крепежные детали и многие другие промышленные изделия.
Достоинством ВТК является то, что его можно проводить при отсутствии контакта между вихретоковым преобразователем (ВТП) и ОК, поэтому его часто называют бесконтактным. Благодаря этому ВТК можно осуществлять при движении ОК относительно ВТП, причем скорость движения при производственном контроле может быть значительной, что обеспечивает высокую производительность контроля. Получение первичной информации в виде электрических сигналов, отсутствие контакта и высокая производительность определяют широкие возможности автоматизации вихретокового контроля.
Дополнительным преимуществом ВТК является то, что на сигналы ВТП практически не влияют влажность, давление и загрязненность газовой среды, радиоактивные излучения, загрязнения поверхности ОК непроводящими веществами, а также простота конструкции ВТП. В большинстве случаев катушки ВТП помещают в защищенный корпус, они устойчивы к механическим и атмосферным воздействиям и представляют собой весьма надежные первичные преобразователи.
Вихретоковый дефектоскоп является универсальным инструментом, позволяя проводить толщинометрию, измерять электропроводность и выполнять дефектоскопию, в том числе и сварных соединений.
Правильно подобранное оборудование позволяет контролировать сварные швы даже через защитное покрытие и выявлять поверхностные и подповерхностные трещины, непровары, поры.
Нашими специалистами был проведен ряд испытаний по контролю сварных соединений образцов вихретоковым дефектоскопом ELOTEST M3 производства Rohmann, Германия (рис. 1, 2).
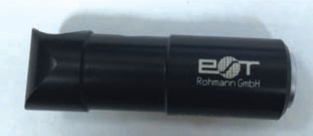

Рис. 3. Специализированный датчик для сварных соединений.
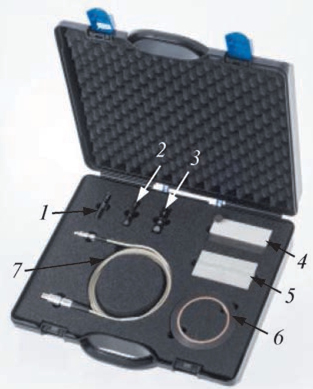

Рис. 4. Набор для контроля сварных соединений: 1 – датчик для контроля толщины покрытий; 2 – датчик для сварных соединений диаметром 12 мм; 3 – датчик для сварных соединений диаметром 16 мм; 4 – стандартный образец для измерения толщины; 5 – стандартный образец для контроля сварных соединений; 6 – кабель для подключения датчиков; 7 – тефлоновая лента.
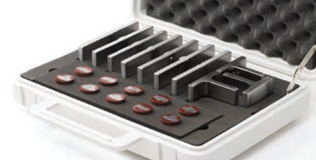

Рис. 5. Набор образцов Sonaspection.
Технические особенности ELOTEST M3:
- частотный диапазон от 10 Гц до 12 МГц;
- типы фильтров: низкочастотный, высокочастотный, полосовой, специальные, оптимизированные для задач с использованием вращающихся датчиков;
- работа с ручными роторами для высокоскоростного контроля отверстий и поверхностей;
- работа в двухчастотном режиме с независимой настройкой по каждой частоте и возможностью микширования сигналов для подавления мешающих факторов (один датчик);
- автоматический выбор рабочей частоты в зависимости от характеристик датчика;
- автоматический выбор предусиления и усиления;
- жидко-кристаллический дисплей с экономичной свето диодной подсветкой, 120×89 мм;
- возможность измерения электропроводности и толщины неэлектропроводящего покрытия толщиной до 1 мм;
- память для хранения настроек и изображений сигналов;
- продолжительная регистрация (ленточная диаграмма) сигналов X и Y в диапазоне от 20 с до 24 ч;
- эксплуатация при температурах от –20 до +50 °С при относительной влажности до 85 % (без конденсации);
- масса 1,2 кг.
Совместно с вихретоковым дефектоскопом ELOTEST M3 использовали специализированный датчик для контроля сварных швов (рис. 3).
Обмотки датчика подключены по мостовой схеме и выполнены перекрестной намоткой. Он был разработан для ручного ВТК сварных швов с возможностью работать через защитное покрытие. Расположение катушек обеспечивает хорошее подавление помех от шва с грубой поверхностью и сводит к минимуму эффект «отвода датчика». Датчик функционирует в диапазоне частот от 100 кГц до 1 МГц, имеет зону контроля 2 мм, глубина проникновения вихревых токов в сталь около 0,2 мм.
Датчик входит в набор для контроля сварных швов, который предлагает компания «ПАНАТЕСТ» (рис. 4). Набор позволяет быстро и эффективно контролировать сварные соединения вне зависимости от их типа, материала, наличия лакокрасочного покрытия и коррозии.
Набор состоит из: двух датчиков с разным радиусом контактной поверхности – 6 и 8 мм, датчика для измерения толщины покрытия, образца с дефектным сварным швом и набором электроизоляционных пластин различной толщины.
Набор соответствует требованиям стандарта DIN EN 1711. Этот набор предназначен для выявления трещин в сварном шве, зоне термического влияния и основном металле изделий, изготовленных из углеродистых и нержавеющих сталей, алюминиевых сплавов. Контроль может осуществляться при производстве и эксплуатации изделия как на море, так и на суше. Диапазон рабочих частот 1кГц–1 МГц. Размеры выявляемых трещин в сварном шве при работе по грубой необработанной поверхности: глубина от 1 мм, длина от 5 мм, толщина покрытия до 2 мм.
Таблица 1. Результаты дефектоскопии пяти стыковых и двух тавровых соединений с имитацией различных дефектов.
Номер образца |
Дефект |
Протяженность дефекта, мм |
|
указанная производителем |
измеренная дефектоскопом |
||
1 |
Трещина |
25 ± 6 |
25 |
1A |
Трещина |
25 ± 6 |
26 |
1B |
Трещина |
25 ± 66 |
23 |
2 |
Трещина в корне шва |
25 ± 66 |
22 |
4 |
Трещина в центре шва, выходящая на поверхность |
25 ± 6 |
26 |
9 |
Непровар в корне шва |
25 ± 6 |
25 |
21 |
Поверхностная трещина с удаленным валиком усиления |
25 ± 6 |
24 |
I. Контроль сварных соединений
В качестве объекта контроля использовали набор образцов Sonaspection (рис. 5). Образцы изготовлены из углеродистой стали и покрыты лаком для защиты от коррозии. Толщина образцов составляет 10 мм.
В комплект набора помимо образцов входят:
- микрошлифы с дефектами;
- описание дефектов, их расположение и параметры;
- комплект сертификационных документов;
- буклет с рентгеновскими снимками дефектных участков.
Образцы представляют собой элементы технических конструкций с искусственными поверхностными дефектами, имеющими известные параметры (размер, расположение). Была проведена дефектоскопия пяти стыковых и двух тавровых соединений с имитацией различных дефектов, приведенных в табл. 1. Контроль выполняли на частоте 100 кГц.
Образец № 1 (рис. 6)
На рис. 6, б представлен микрошлиф стыкового сварного шва с поверхностной трещиной, идущей вглубь металла параллельно сварному соединению. Такие трещины могут находиться как в сварном соединении, так и в зоне термического влияния.
На рис. 6, в показана рентгенограмма, на которой трещина отображается тонкими темными волнистыми линиями, часто прерывистыми.
![]() ![]() a) |
![]() ![]() в) |
![]() ![]() б) |
![]() ![]() г) |
Рис. 6. Образец № 1: а – внешний вид образца; б – микрошлиф с дефектом; в – рентгенограмма дефектной области; г – сигнал от вихретокового преобразователя в дефектной области |
Шов был просканирован ВТП, и в дефектной области на дисплее дефектоскопа был получен сигнал, амплитуда которого превысила предустановленный пороговый уровень в форме окружности (рис. 6, г). Пороговый уровень был выставлен по образцу с риской глубиной 1 мм. Измеренное дефектоскопом значение длины трещины составило 25 мм.
Образец № 2 (рис. 7). Трещина в корне шва, контроль со стороны корня
На рис. 7, б представлен микрошлиф стыкового сварного шва. В шве со стороны корня имеется трещина, идущая параллельно соединению. На рис. 7, в показана рентгенограмма, на которой трещина отображается темными тонкими неровными линиями, расположенными в центре или ближе к кромкам корня шва, обозначенного светлой областью на изображении. Отличается от непровара в корне шва своей извилистой формой.
![]() ![]() a) |
![]() ![]() в) |
![]() ![]() б) |
![]() ![]() г) |
Рис. 7. Образец № 2: а – внешний вид образца; б – микрошлиф с дефектом; в – рентгенограмма дефектной области; г – сигнал от вихретокового преобразователя в дефектной области |
Шов был просканирован ВТП, и в дефектной области на дисплее дефектоскопа был получен сигнал, амплитуда которого превысила предустановленный пороговый уровень (рис. 7, г). Измеренное значение длины трещины составило 22 мм.
Образец № 4 (рис. 8). Трещина в валике усиления
На рис. 8, б представлен микрошлиф сварного шва. В валике усиления сварного соединения имеется выходящая на поверхность трещина.
На рис. 8, в показана рентгенограмма, на которой трещина отображается темными тонкими неровными линиями, идущими параллельно или вдоль центральной линии сварного соединения. Данный дефект более четко различим на рентгенограммах, чем подповерхностные трещины.
![]() ![]() a) |
![]() ![]() в) |
![]() ![]() б) |
![]() ![]() г) |
Рис. 8. Образец № 4: а – внешний вид образца; б – микрошлиф с дефектом; в – рентгенограмма дефектной области; г – сигнал от вихретокового преобразователя в дефектной области |
Амплитуда сигнала на дисплее дефектоскопа в дефектной области превысила пороговый уровень, рис. 8, г. Измеренное значение длины трещины составило 26 мм.
Образец № 9 (рис. 9). Непровар в корне шва, контроль со стороны корня
На рис. 9, б представлен микрошлиф сварного шва с непроваром со стороны корня сварного соединения.
На рентгенограмме рис. 9, в непровар отображается очень тонкой темной линией, идущей вдоль границы светлого изображения – корня сварного шва.
![]() ![]() a) |
![]() ![]() в) |
![]() ![]() б) |
![]() ![]() г) |
Рис. 9. Образец № 9: а – внешний вид образца; б – микрошлиф с дефектом; в – рентгенограмма дефектной области; г – сигнал от вихретокового преобразователя в дефектной области |
Контроль проводили со стороны корня шва. Амплитуда сигнала на дисплее дефектоскопа в дефектной области превысила пороговый уровень (рис. 9, г). Протяженность трещины равна 25 мм.
Образец № 21 (рис. 10). Поверхностная трещина в шве с удаленным валиком усиления
На рис. 10, б представлен микрошлиф сварного шва с удаленным валиком усиления и трещиной, идущей параллельно сварному шву. Направление таких трещин может меняться. Они могут возникать в результате внешних нагрузок или при усадке наплавленного металла при охлаждении.
На рентгенограмме рис. 10, в трещина отображается темными неровными линиями, расположенными близко друг к другу и на расстоянии, зависящем от параметров трещины.
![]() ![]() a) |
![]() ![]() в) |
![]() ![]() б) |
![]() ![]() г) |
Рис. 10. Образец № 21: а – внешний вид образца; б – микрошлиф с дефектом; в – рентгенограмма дефектной области; г – сигнал от вихретокового преобразователя в дефектной области |
Амплитуда сигнала на дисплее дефектоскопа в дефектной области превысила пороговый уровень (рис. 10, г). Протяженность трещины равна 24 мм.
Образец № 1A (рис. 11). Трещина в зоне термического влияния
На рис. 11, б представлен микрошлиф таврового сварного шва. В шве имеется трещина, идущая вглубь металла параллельно сварному соединению. Такие трещины могут находиться как в сварном соединении, так и зоне термического влияния.
На рентгенограмме рис. 11, в трещина отображается темными волнистыми линиями, часто прерывистыми.
![]() ![]() a) |
![]() ![]() в) |
![]() ![]() б) |
![]() ![]() г) |
Рис. 11. Образец №1А: а – внешний вид образца; б – микрошлиф с дефектом; в – рентгенограмма дефектной области; г – сигнал от вихретокового преобразователя в дефектной области |
Амплитуда сигнала на дисплее дефектоскопа в дефектной области превысила пороговый уровень (рис. 11, г). Протяженность трещины равна 26 мм.
Образец № 1B (рис. 12)
На рис. 12, б представлен микрошлиф таврового сварного шва с трещиной, идущей вглубь металла параллельно сварному соединению. Такие трещины могут находиться как в сварном соединении, так и в зоне термического влияния.
На рентгенограмме рис. 12, в трещина отображается темными волнистыми линиями, часто прерывистыми.
![]() ![]() a) |
![]() ![]() в) |
![]() ![]() б) |
![]() ![]() г) |
Рис. 12. Образец № 1B: а – внешний вид образца; б – микрошлиф с дефектом; в – рентгенограмма дефектной области; г – сигнал от вихретокового преобразователя в дефектной области |
Амплитуда сигнала на дисплее дефектоскопа в дефектной области превысила пороговый уровень (рис. 12, г). Протяженность трещины равна 23 мм.
II. Контроль околошовной зоны
Для контроля околошовной зоны был использован ротор, работающий на плоских или слабокриволинейных участках.
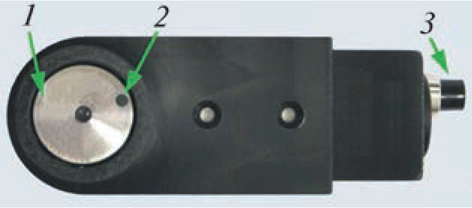

Рис. 13. Мини-ротор для контроля плоскостей: 1 – вращающийся диск; 2 – датчик; 3 – кнопка включения.
При использовании плоскостных роторных преобразователей (рис. 13) достигается высокая производительность контроля. Катушка имеет небольшие размеры (диаметр 1,5–3 мм), что обеспечивает высокую чувствительность при выявлении дефектов любой ориентации. Ширина полосы сканирования равна диаметру диска. Кроме того, значительно уменьшается вероятность пропуска дефектов по сравнению с карандашными и многоэлементными датчиками за счет многократного пересечения датчиком дефектного участка за один проход. Тем самым, имея один канал ручного дефектоскопа и роторный датчик, можно в некоторых случаях отказаться от применения многоэлементных преобразователей.
Максимальная скорость вращения может достигать 2700 об/мин, что позволяет перемещать ротор со скоростью 70 мм/с. Произ водительность контроля при диаметре диска 50 мм составляет 35 см2/с.
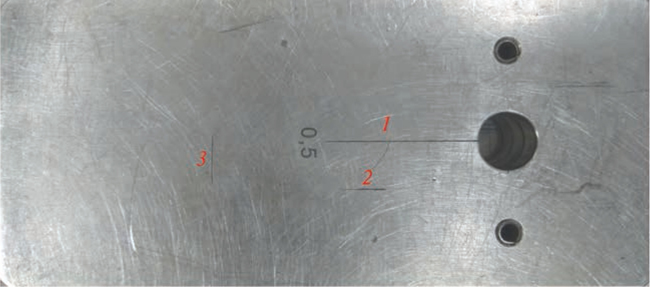

а)
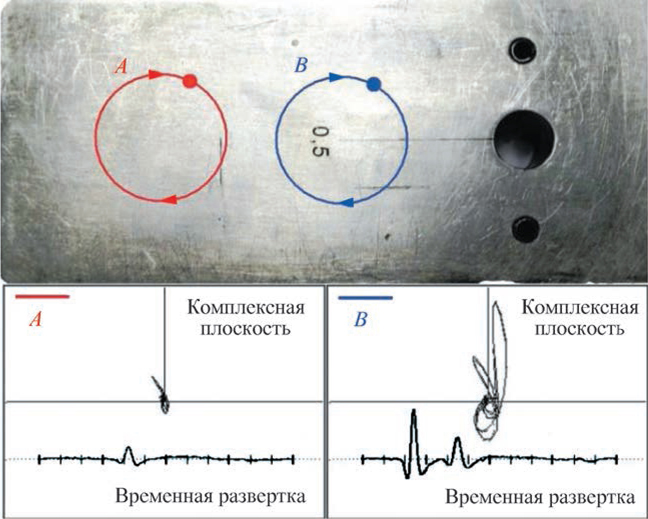

б)
Рис. 14. Расположение дефектов на алюминиевом образце (а) и сигналы на экране прибора в точках A и B (б)
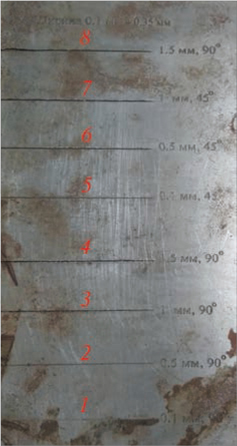

Рис. 15. Образец из стали 20 с рисками.
Испытания на образце из алюминия
Контроль выполняли на алюминиевой пластине толщиной 6 мм с нанесенными на ее поверхность тремя рисками (рис. 14, а). Параметры рисок указаны в табл. 2. Рабочая частота преобразователя 400 кГц.
Таблица 2. Геометрические параметры рисок на алюминиевом образце.
№ |
Глубина, мм |
Длина, мм |
1 |
0,5 |
25 |
2 |
0,2 |
4 |
3 |
0,2 |
8 |
В рамках испытания проводили сплошной контроль поверхности. В точках А и В были получены сигналы от рисок, приведенные на рис. 14, б. Сигналы представлены на комплексной плоскости и временной развертке.
Испытания на стальном образце
На втором этапе испытаний использовали образец из стали 20 толщиной 2 мм с вертикальными и наклонными рисками № 1–8 различной глубины (рис. 15). Геометрические параметры рисок указаны в табл. № 3.
Таблица 3. Геометрические параметры рисок на образце из стали 20.
№ п/п |
Глубина, мм |
Ширина, мм |
Угол между плоскостью риски и поверхностью образца, ° |
Длина, мм |
1 |
0,1 |
0,1 – 0,35 |
90 |
60 |
2 |
0,5 |
0,1 – 0,35 |
90 |
60 |
3 |
1,0 |
0,1 – 0,35 |
90 |
60 |
4 |
1,5 |
0,1 – 0,35 |
90 |
60 |
5 |
0,1 |
0,1 – 0,35 |
45 |
60 |
6 |
0,5 |
0,1 – 0,35 |
45 |
60 |
7 |
1,0 |
0,1 – 0,35 |
45 |
60 |
8 |
1,5 |
0,1 – 0,35 |
45 |
60 |
Чувствительность и пороговый уровень срабатывания сигнализации были настроены по прямой № 1 (рис. 16, а) и наклонной № 5 (рис. 16, д) рискам.
Контроль листа был выполнен за один проход поперечным по отношению к направлению рисок перемещением сканера.
Сигналы, полученные от каждой риски, представлены на рис. 16.
Заключение
Результаты проведенной работы показали надежность и высокую производительность выявления трещин в сварных швах вихретоковым методом. Были выявлены все трещины в сварном шве и зоне термического влияния.
Специализированные вихретоковые датчики позволяют отстроиться от влияния мешающих факторов и работать по грубой необработанной поверхности сварного шва даже через защитное покрытие.
Использование одноканального дефектоскопа с роторным датчиком обеспечивает сканирование поверхности зоны контроля, равной диаметру диска. Значительно уменьшается вероятность пропуска дефекта независимо от его ориентации по сравнению с «карандашными» или даже многоэлементными датчиками за счет многократного пересечения дефектного участка преобразователем. Производительность контроля зоны может достигать 35 см2/с.
Статья опубликована в журнале "Территория NDT", апрель–июнь 2017.
Загрузить статью в формате PDF...